
Empire WWTP Solids Improvements Enhance Operations
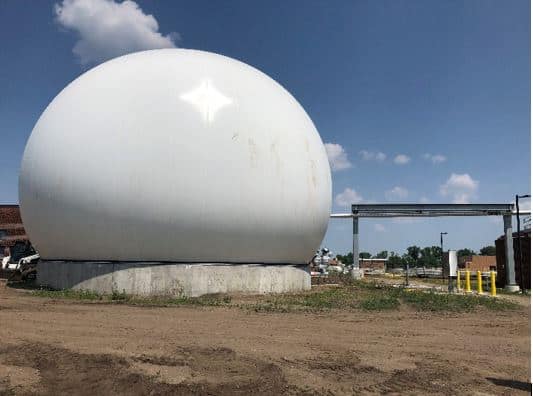
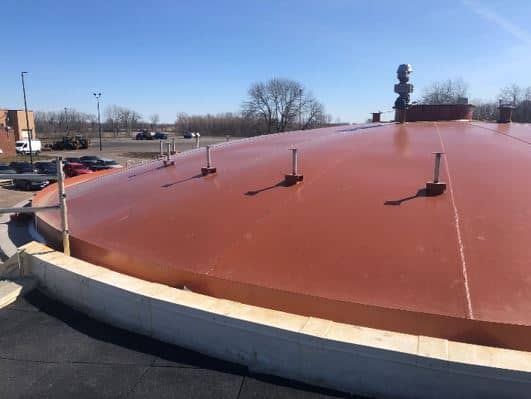
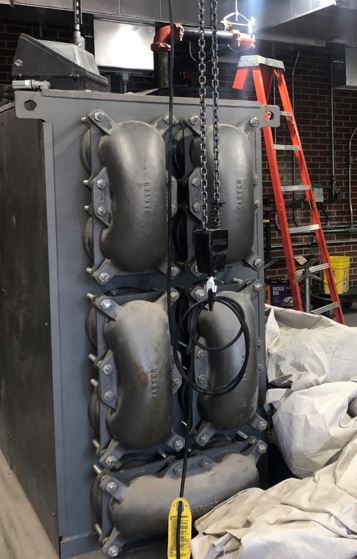
- Local Governments
- Public Sector
Market
- Engineering
- Wastewater
- Water
Services
- Metropolitan Council Environmental Services, Farmington, Minnesota
Locations
Challenge: The Metropolitan Council Environmental Services (MCES) Empire Wastewater Treatment Plant (WWTP) needed to increase digester capacity and biogas storage and provide operator flexibility to take down one digester annually. The WWTP has three primary anaerobic digesters (Digesters 1, 2, and 5) with fixed steel covers and two secondary digesters (Digesters 3 and 4) with floating covers. All digesters are 60 feet in diameter and have three internal draft tube mixers. Digester 3, a secondary digester, can be heated with a tube-in-tube heat exchanger, allowing it to operate as a primary when another primary is down for maintenance.
Increase Digester Capacity and Enhance Storage
The design replaced the floating covers on Digesters 3 and 4 with fixed covers, added a fifth tube-in-tube heat exchanger to allow Digester 4 to operate as a primary, and installed a 3/4 membrane sphere at grade for 44,000 cubic feet of biogas storage. A jet mix system was chosen over internal draft tube mixers for the secondary digesters, enabling continued mixing even as sludge levels drop lower than what internal mixers would allow. Radar level sensors, backed by differential pressure transducers, are the primary method for level measurement in each digester, though they cannot measure foam. For the newly installed secondary digesters, a laser level transmitter was selected for its foam measurement capability. The WWTP plans to evaluate its performance and may transition other radar sensors to this technology. Additionally, the new fixed covers will feature an EPDM membrane roof over insulation board to minimize heat loss.
Upgrades and Energy Efficiency
In addition to the digester conversion, improvements included replacing five boilers with three new high-efficiency boilers (7,080 MBH each), upgrading the sludge loadout system with new feed pumps, adding a 3-acre covered storage for cake, installing a new flare, and adding a 1000 kW Combined Heat and Power (CHP) engine with gas cleaning for moisture, sulfur, and siloxane removal. Phase I construction was completed in 2024, and Phase II is currently underway. The total construction cost for both phases is approximately $40 million.
Benefit: The Empire WWTP improvements collectively enhance the plant’s operational efficiency, flexibility, and sustainability, positioning it well for future challenges and growth.